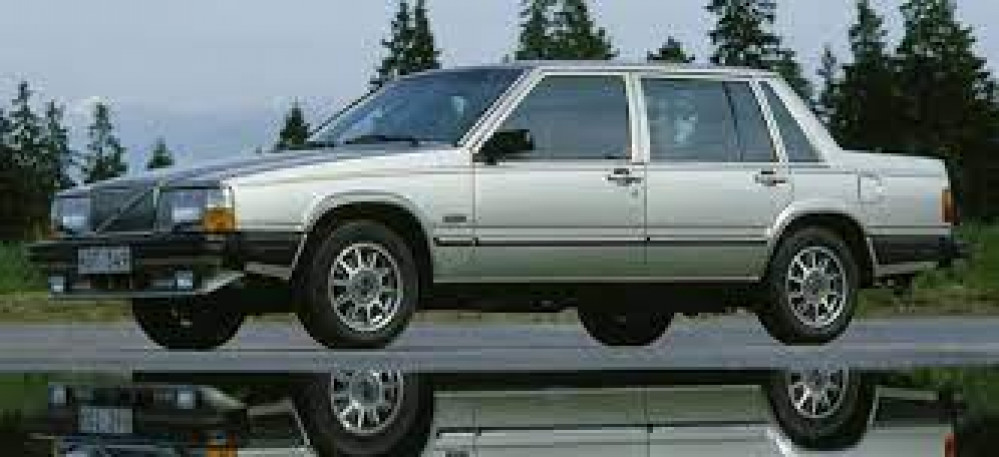
Volvos in space – a spring cleaning challenge
Recommendations: 352
About the Project
I decided to join the fun this year as well, even with failure of last year project which still isn’t finished. First, couple of words explaining the title. The project is about building and painting (and narrating history) of Pathfinder Chimera class spaceship designed by 2nd dynasty and funded in Kickstater campaign some 18 months ago (IIRC). It is now available for purchase on Myminifactory page (address in first project entry). Now, the ship is extremely blocky, true glorification of the shape of a brick. Since I’m old enough to remember the 80’ as it was yesterday, it instantly brought Volvos 240 and 740 to mind. Those glourios Sweedish cars were designed using only one tool: setsquare! Since designer of the model is Australian but lives in Sweden (!!!) there was no way back from association. For me the Chimera class and Chimera Subclass were all designed by spaceship architects from Volvo Heavy Space Industry PLC and built by shipyards owned by that company or working on its licence.
Related Genre: Science Fiction
Related Contest: Spring Clean Hobby Challenge (Old)
This Project is Active
Slowly, but surely
I spent most of this year’s Christmas/New Year period adding to my Chimera Pathfinder. This time I focused on the exterior: added four mighty Rolls Royce Dumbledore engines and the rest of the glasswork. I still need to print and paint the manoeuvring thrusters and radio/sensor array, I also lost somewhere a detailing piece from the ramp, I’m quite sure I had it painted but can’t find it now.
This is current state of the build.
Windshield
Inspired by one of the guys over the 2ndDynasty’s discord, I prepared sheet of acetate to use for translucent surfaces in my ship.
The process is easy enough – 0,7 mm acetate sheet airbrushed through a stencil with matt varnish mixed with a drop of blue wash. Nothing ground-breaking, but always more interesting than simple translucent piece, I guess.
Deck 1 is ready for operation
I finished the hold deck.
The AAR is as follows:
1. Black base coat,
2. Stipple desaturated green (I used craft paints and mixed black, white and forest green). I did a couple of passes with the stippling brush applying gradually lighter coats. The colour should concentrate in the centre of panels and avoid deeper recesses.
3. Paint-on details like hazard stripes, fire extinguishers and all the gizmos littering the inside of the ship.
4. Decals. I have several sheets of DIY decals with some symbols and H&S signs. Very useful and easy to do by simply finding them out on the Internet.
5. Layer of varnish. I use Pledge floor polish for those bigger projects. It is cheap and works good over the airbrush.
6. Overall thick oil wash of 50/50 burnt umber and mars black. Then when it dries a bit of course wipe it off.
7. Black pinwash around panels and details.
8. Black rim on the top surfaces of the walls.
Work in progress
I’m working my way through the lowest deck. Today I finished decaling and detailing it. Now I need to leave it for a night to dry properly and tomorrow some washes and maybe OSL would finish my work in the hold.
Inside colours
Today I did some work trying colour schemes for the inside of the ship. I started with the lowest deck (hold) and came up with what you see bellow.
I wanted to use some real life reference and watched bunch of films over on YT showing modern sea-going ships, but they all looked sterile clean on the inside and that look doesn’t sell well on 3d print.
In the end I decided to go with quite heavily beaten up look on lower deck and a bit tidier (but far from from presttine) higher up. The colors will be the same all over.
C&C appreciated.
This brick will fly!... Eventually
Now, that was a break… At some point I stopped taking pictures of following steps and thus stopped reporting on progress. That said, I haven’t stopped working on the ship. Bellow you’ll see some photos I dug from my phone, they document various steps of progress, see descriptions.
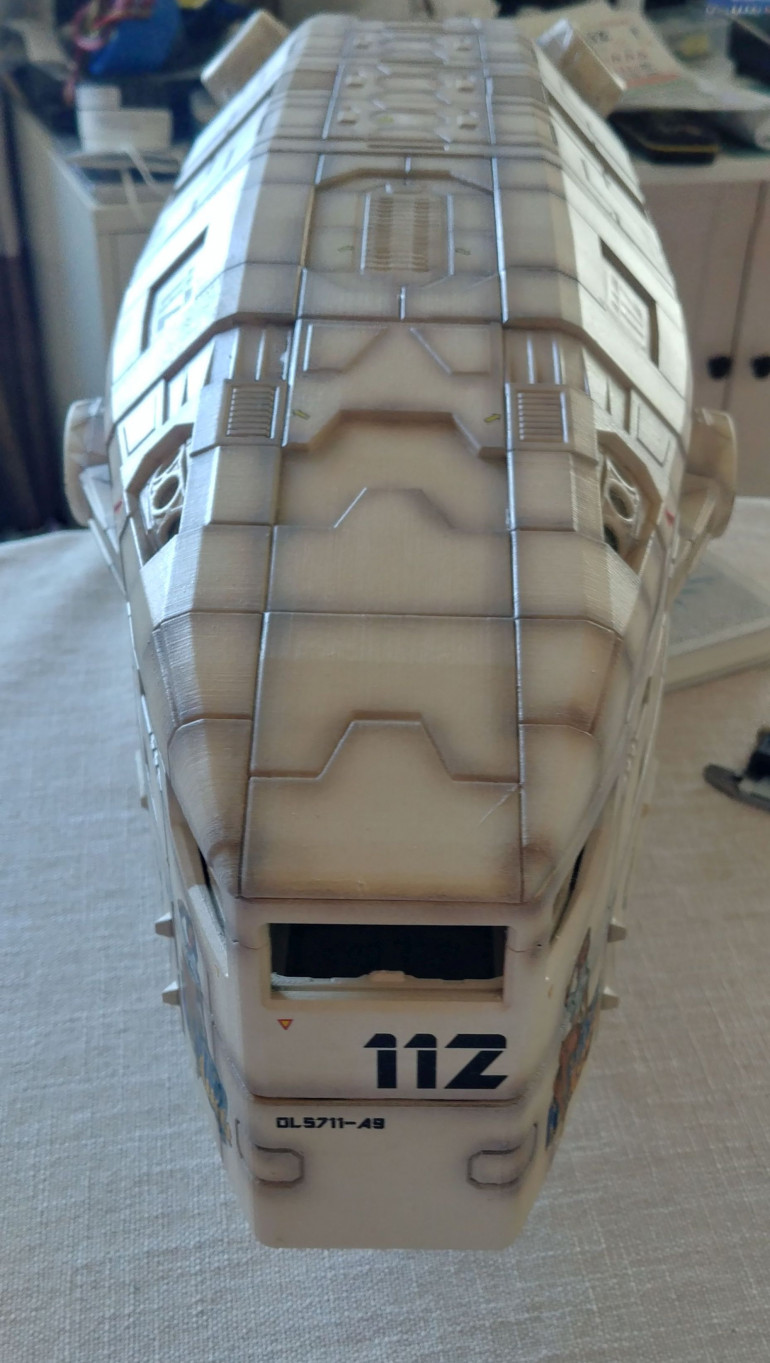
Progress report 10.05.2021
Progress report 10.05.2021
I had a week off, but then I managed to push the work quite a bit further.
Pictures bellow tell whole story of pre-shading and applying final colour of the fuselage.
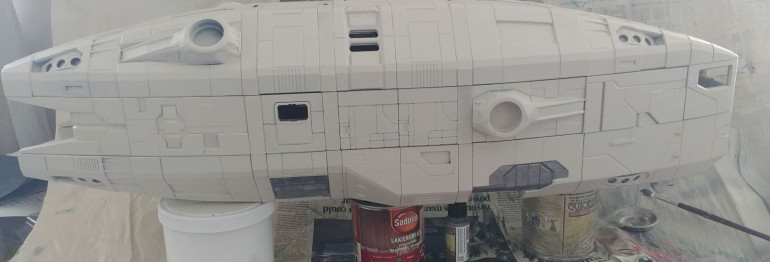
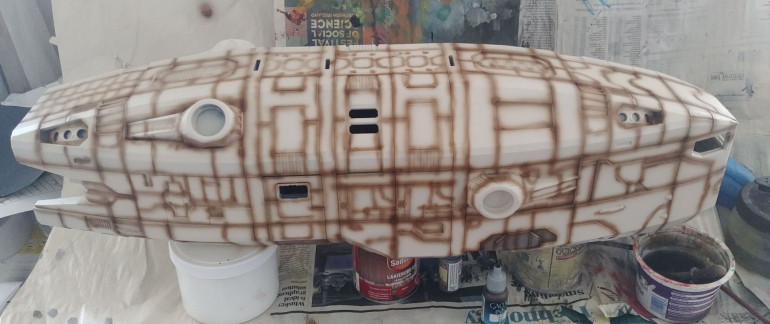
I think, lost one photo somewhere. Next step was to accentuate centre of each panel with white ink. This is where I had do spend additional time tiding speia lines.
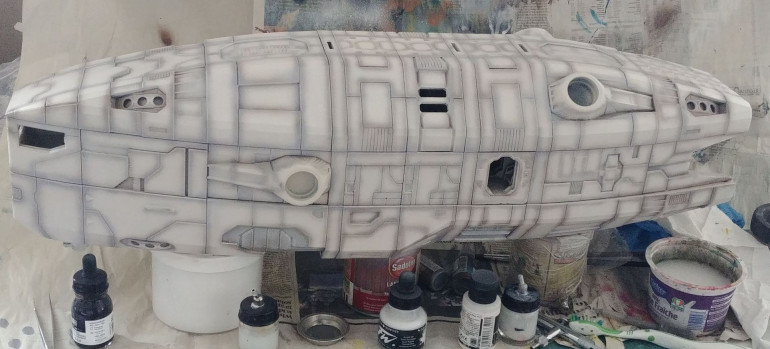
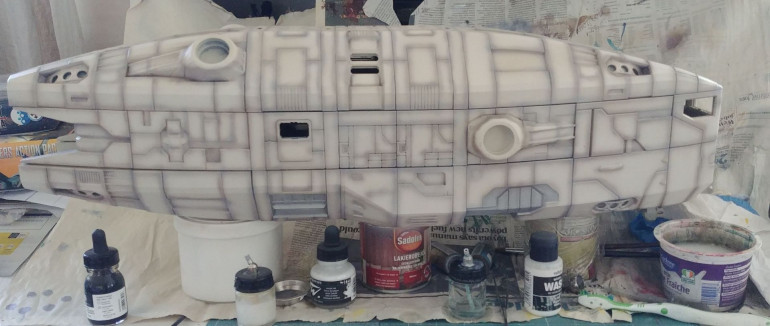
Progress report 25.04.21
I did quite a lot of work last week, but don’t have much to show for it (photo-wise anyway). I’m only two build plates away from having everything printed out and I painted all the shell (inside and out) with the spray, I skipped the gesso on two lower decks as it wasn’t playing nice with tolerances of the model.
Just one quick photo:
Progress report 17.04.21
Well, printing is progressing steadily, but I had some stupid misprints – like the one where I put draining hole ideally on the same level and it was enough for the peel forces to tear the model in half…
Also I need to limit final curing time, because the resins tends to get too brittle and break while I push the connectors in…
Also, we had beautiful day today so I painted the outer shell of the top deck.
Detailed inventory and printing plan
I compared whatever pictures of the Chimera Pathfinder I could find with parts I had printed to date. I came to some conclusions on what I still need to print. Bellow you’ll see visualisation of what is needed in case I decided to print original arrangement of the interior, I’m still not certain I want to.
Not so humble beginning
True to founding idea of Spring Cleaning Challenge, my project is ongoing for quite some time, at least a year.
That means on the one hand, that I have some work done, and on the other that my initial enthusiasm has already burnt out.
Therefore let me start with a bit of inventory:
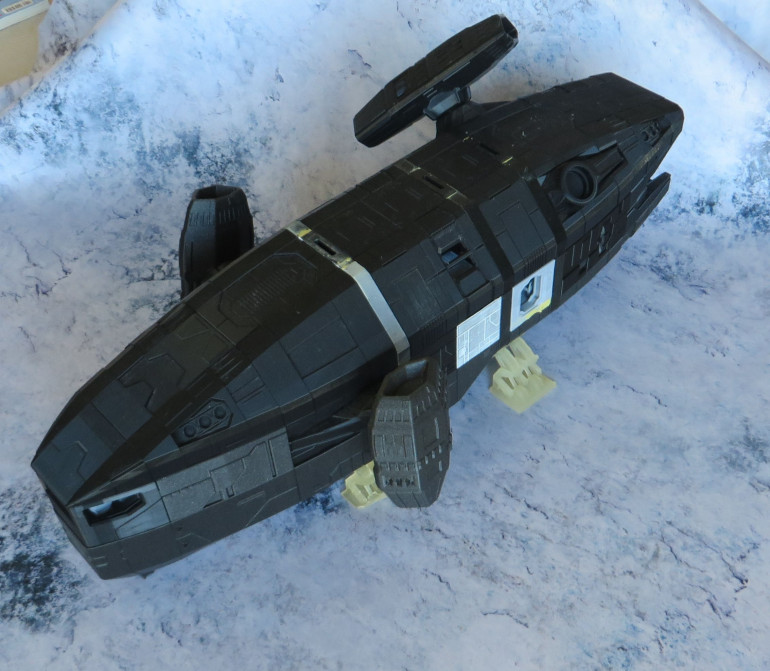
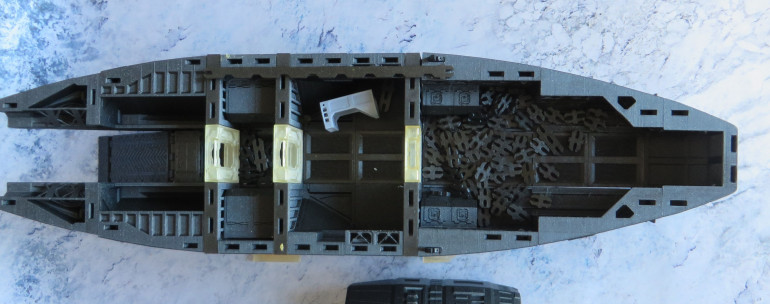
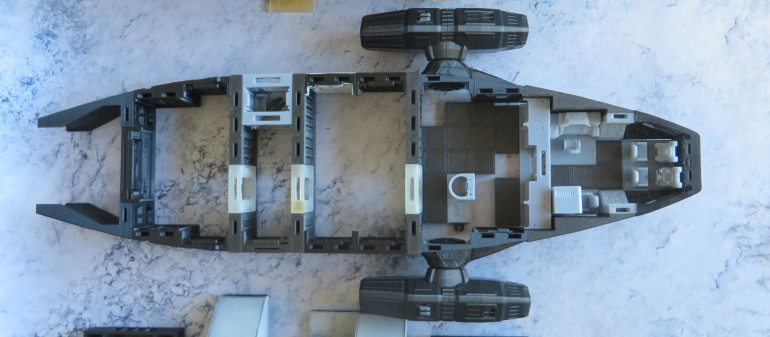
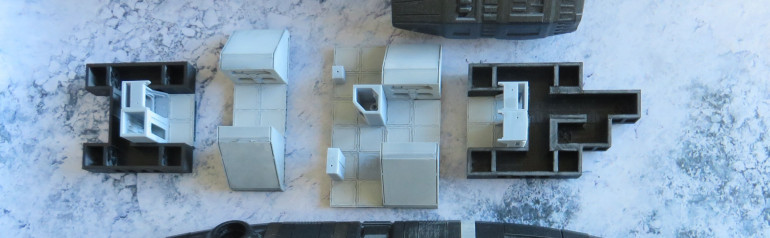
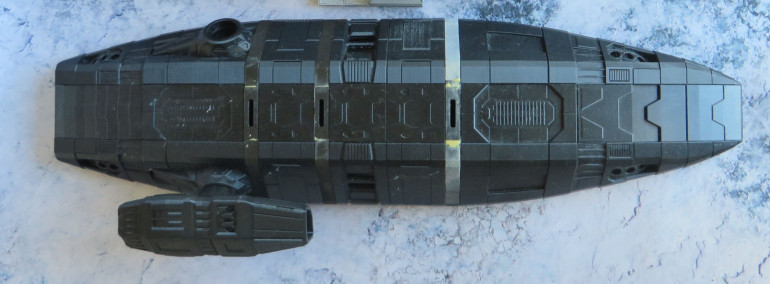
As for technical side of things; all the external parts, most of the floors and bunks on the top deck were printed on my Prusa I3 mk3 at .15 mm layers with 15% infill, with exception for bunks which have varying layer heights from 0.15 to .3 for speed. I used Amazon branded filament and Prusament (both PLA of course).
The parts printed on SLA printer (Elegoo Mars) are printed on normal setting so .05 mm layers, Elegoo resin, some translucent and some grey.
You may also notice that I have cut out detailed parts of bulkheads and printed them on SLA while rest of the part was printed on FDM.
Oh, and the model can be purchased HERE.